Signs You Need Professional Packaging Machine Repair Right Away
Signs You Need Professional Packaging Machine Repair Right Away
Blog Article
Quick and Reliable Packaging Device Repair Work Services to Reduce Downtime
In the competitive landscape of production, the performance of packaging operations hinges on the integrity of machinery. Quick and trusted repair work services are crucial in alleviating downtime, which can lead to substantial operational setbacks and monetary losses.
Value of Timely Services
Timely fixings of product packaging equipments are crucial for maintaining functional effectiveness and lessening downtime. In the hectic setting of manufacturing and product packaging, also minor malfunctions can result in significant hold-ups and efficiency losses. Addressing problems quickly makes sure that devices run at their ideal capability, thus securing the flow of operations.
Moreover, prompt and normal upkeep can protect against the rise of minor issues right into major malfunctions, which usually sustain higher repair prices and longer downtimes. A proactive method to maker fixing not only maintains the integrity of the equipment but likewise enhances the general reliability of the assembly line.
Additionally, timely repairs add to the durability of product packaging machinery. Devices that are serviced promptly are less likely to struggle with excessive damage, permitting businesses to optimize their investments. This is specifically crucial in markets where high-speed packaging is necessary, as the requirement for constant performance is vital.
Benefits of Reliable Company
Reliable service companies play an essential role in making sure the smooth operation of packaging machines. Their experience not only boosts the performance of repairs but likewise contributes significantly to the durability of devices.
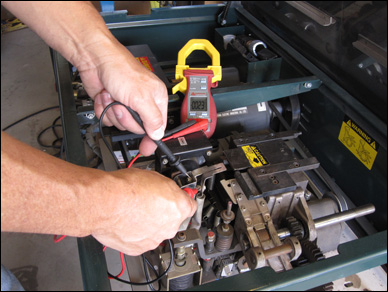
Furthermore, a trusted provider provides comprehensive support, including training and support for staff on machine procedure and maintenance finest methods. This not only empowers workers but additionally cultivates a society of security and effectiveness within the organization. In general, the advantages of involving reliable service providers prolong beyond prompt repair services, positively impacting the entire operational operations of packaging procedures.
Common Product Packaging Device Problems
In the world of packaging operations, different problems can jeopardize the efficiency and performance of equipments (packaging machine repair). An additional common concern is imbalance, which can cause jams and uneven product packaging, influencing product high quality and throughput.
Electrical issues can additionally interrupt packaging procedures. Defective wiring or malfunctioning sensors may lead to unpredictable maker habits, causing hold-ups and increased operational expenses. In addition, software program my explanation problems can hinder the equipment's programming, causing functional inefficiencies.
Inconsistent item flow is an additional critical concern. This can occur from variations in item size, form, or weight, which might influence the equipment's capacity to take care of products properly. Ultimately, insufficient training of drivers can intensify these troubles, as inexperienced workers may not identify very early indications of malfunction or might misuse the equipment.
Dealing with these typical product packaging equipment problems without delay is essential to preserving performance and making certain a smooth operation. Regular inspections and positive upkeep can dramatically alleviate these worries, fostering a trusted packaging setting.
Tips for Lessening Downtime
To decrease downtime in product packaging procedures, carrying out a proactive maintenance method is important. On a regular basis scheduled maintenance checks can determine prospective issues before they rise, guaranteeing devices operate effectively. Establishing a routine that includes lubrication, calibration, and inspection of vital elements can substantially reduce the regularity of unexpected malfunctions.
Training personnel to operate machinery properly and acknowledge very early warning indicators of breakdown can likewise play a vital function. Empowering operators with the knowledge to perform fundamental troubleshooting can avoid minor problems from creating significant delays. Maintaining an efficient inventory of necessary spare components can quicken repair work, as waiting for components can lead to extensive downtime.
Additionally, recording equipment efficiency and maintenance activities can assist identify patterns and persistent issues, allowing for targeted interventions. Integrating innovative surveillance modern technologies can provide real-time information, enabling predictive upkeep and decreasing the risk of abrupt failings.
Finally, promoting open interaction between drivers and upkeep teams makes visit this site certain that any type of abnormalities are immediately reported and addressed. By taking these positive measures, businesses can improve functional efficiency and significantly decrease downtime in product packaging procedures.
Choosing the Right Repair Work Solution
Picking the suitable fixing solution for packaging devices is a critical decision that can dramatically impact functional performance. Begin by evaluating the service provider's experience with your certain type of product packaging equipment.
Following, consider the company's online reputation. Looking for responses from other services within your sector can offer insights into reliability and high quality. Accreditations and partnerships with recognized tools producers can also suggest a commitment to excellence.
Additionally, examine their reaction time and schedule. A company who can offer prompt assistance decreases downtime and their website keeps production circulation consistent. It's also critical to make inquiries about warranty and solution warranties, which can show the self-confidence the service provider has in their job.

Verdict
Finally, the importance of fast and reliable product packaging device repair service services can not be overstated, as they play an important role in minimizing downtime and guaranteeing functional efficiency. By focusing on timely repair work and selecting reputable solution carriers, companies can effectively address typical issues and preserve performance. Carrying out proactive upkeep practices and purchasing staff training additional improves the durability of product packaging equipment. Ultimately, a tactical strategy to fix solutions cultivates a more resistant manufacturing atmosphere.
Prompt fixings of product packaging devices are critical for maintaining operational efficiency and minimizing downtime.Additionally, timely repair work add to the longevity of product packaging machinery. On the whole, the benefits of involving reputable service providers prolong beyond prompt repair work, favorably affecting the entire functional operations of product packaging processes.

Report this page